Choosing the right materials is key to managing your construction budget. One vital fact to remember: precast concrete planks typically cost between $25 and $40 per square foot. Our article will break down the costs of precast concrete, showing you how these figures come together and where you can save money.
Key Takeaways
- Precast concrete planks typically range from $25 to $40 per square foot, but costs can be influenced by factors like shape, size, and delivery.
- Additional expenses that affect the overall cost include excavation ($2 to $15 per square foot), engineering fees (5% to 15% of total project costs), installation, finishing costs ($5 to $10 per square foot for basic finishes), and design complexity.
- Ways to potentially lower precast concrete plank costs include getting multiple quotes from suppliers, choosing less expensive materials without sacrificing quality, opting for standard designs and finishes, and hiring experienced contractors who understand efficient construction practices.
Factors that Influence the Cost of Precast Concrete
The cost of precast concrete is influenced by various factors such as shape, dimensions, weight, delivery, excavation, engineering fees, installation, finishing and design. These factors can contribute to the overall expenses of a precast concrete project.
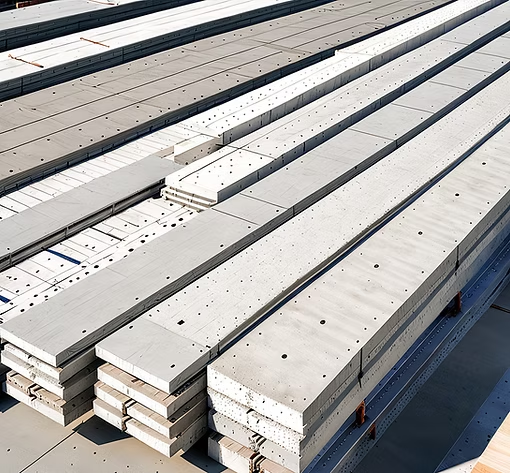
Shape
Unique shapes in precast concrete planks can drive up the price due to the complexity of their design and manufacturing. Curves, angles, or custom patterns require specific molds and additional engineering expertise.
These specialized requirements often translate into higher production costs as they may involve more intricate reinforcement or unique concrete mixes tailored to ensure structural integrity.
Complexity in shape also impacts handling and transportation. Stronger or differently shaped planks might need special lifting equipment on-site for safe installation without damage, leading to increased labor costs.
With more elaborate designs comes the necessity of precise coordination between teams—a factor that reflects directly in total expenses. Next, let’s consider how dimensions affect precast concrete plank cost.
Dimensions
Transitioning from the shape of precast concrete to its dimensions, it’s crucial to consider that the size and measurements of precast concrete panels, slabs, beams, and other components greatly impact their cost.
The physical dimensions directly affect factors such as weight, material usage, transportation requirements, and installation labor.
The larger the dimensions of a precast concrete piece or panel, the higher its material costs and weight due to increased materials needed for production. This subsequently influences shipping expenses for transportation from the manufacturing facility to the construction site.
Weight
After considering the dimensions of precast concrete, it’s essential to evaluate the weight aspect, as this greatly influences the overall cost. The weight of precast concrete components is a significant factor in determining transportation costs and installation expenses, impacting the total project budget.
Heavier panels or planks may require more substantial equipment for handling and could increase labor expenses during installation. The weight of precast concrete products can also affect foundation design and construction costs, contributing to variations in overall project expenditures.
Additionally, understanding the weight of precast concrete is crucial for structural considerations as it impacts load-bearing capacities and engineering requirements. Moreover, architects and designers must take into account the weight distribution when planning for complex structures or multistory buildings to ensure stability and safety.
Delivery
Delivery costs for precast concrete products can vary based on factors such as the distance from the manufacturer, the size and weight of the products, and any special handling requirements.
Typically, delivery expenses for precast concrete planks range from $100 to $500 per load, depending on transportation fees and access to the construction site. It’s essential to consider these costs when budgeting for a precast concrete project to ensure an accurate estimation of overall expenses.
When planning your precast concrete project, it’s crucial to factor in delivery costs alongside other expenses like material and installation. This will help provide a comprehensive overview of your budget before proceeding with your construction project.
Excavation
Excavation for precast concrete involves preparing the ground by digging and leveling to create a stable base. The excavation phase is crucial as it directly impacts the overall cost of the project, with costs estimated to range from $2 to $15 per square foot.
Factors influencing these costs include soil conditions, depth of excavating needed, debris removal, and any necessary site preparation prior to installation.
The expense of excavation may vary based on location and accessibility. It’s essential to consult with experienced contractors who can conduct a thorough assessment of the site before starting this foundational step.
Engineering Fees
Engineering fees for precast concrete can vary depending on the project’s complexity and specific requirements. The cost of engineering services typically ranges from 5% to 15% of the total project costs, covering aspects such as design development, structural analysis, and quality control.
Factors influencing engineering fees include the size and scope of the project, site conditions, material specifications, and compliance with building codes and standards.
It’s essential to consider that engineering fees are a crucial aspect of precast concrete construction expenses. Properly budgeting for these costs ensures that the project is executed efficiently while meeting safety and regulatory requirements.
Installation
After factoring in engineering fees, the next consideration is the installation of precast concrete elements. The cost of installing precast concrete can vary widely based on factors such as panel size, weight, and complexity.
On average, the installation cost ranges from $20 to $30 per square foot for smaller panels and around $15 to $25 per square foot for larger panels. Additional costs may also be incurred for specialized equipment or labor requirements depending on the project’s scope and location.
To ensure a successful installation process, it’s essential to engage experienced contractors who are familiar with handling and placing precast concrete components efficiently. Proper planning and coordination between all parties involved are crucial to minimize any potential delays or complications during the installation phase, ultimately contributing to keeping overall project costs under control.
Finishing
Finishing precast concrete can add to the overall cost, with expenses ranging from $5 to $10 per square foot. This cost might vary depending on the type of finish chosen, such as smooth or textured finishes.
Additional treatments like sealing and staining could also increase the total cost by an average of $2 to $4 per square foot, adding a decorative touch or enhancing durability.
The finishing process entails careful attention to detail and precision application techniques, ensuring a high-quality final product that aligns with the project’s specifications.
Design
Design plays a crucial role in influencing the cost of precast concrete structures. The complexity and intricacy of the design can significantly impact the overall expenses. Custom designs and intricate patterns may incur higher engineering fees due to the specialized expertise required for implementation, potentially adding additional costs to the project.
Moreover, unique design requirements may also increase manufacturing costs as they demand precision and attention to detail, leading to higher production expenses.
When it comes to precast concrete construction, simple and efficient designs can help minimize costs while maintaining structural integrity. By opting for straightforward and practical designs that reduce material waste during production, developers can effectively lower expenses without compromising on quality or durability.
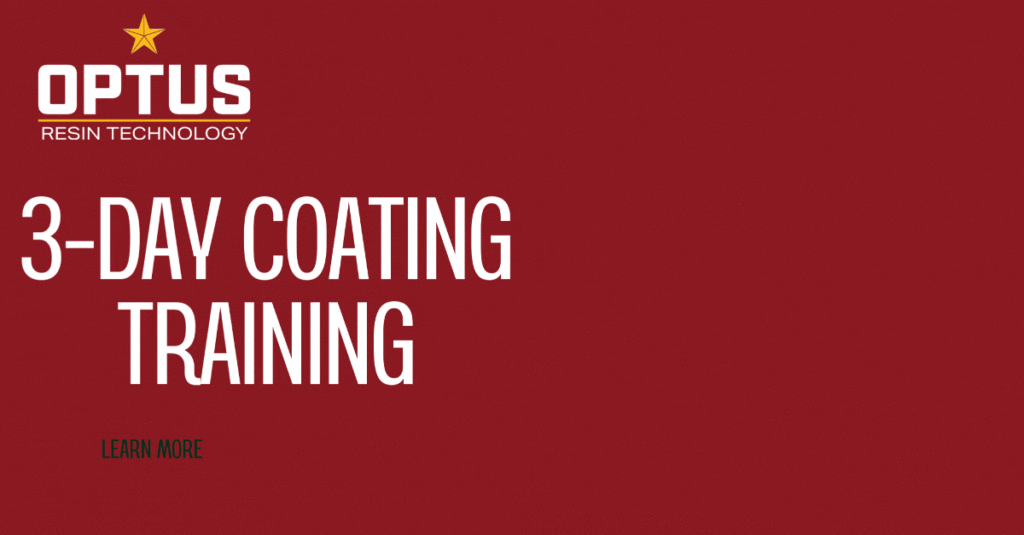
Comparison of Precast Concrete and Poured Concrete Walls
Precast concrete walls tend to cost less per square foot compared to poured concrete walls, making them a more cost-effective option for construction projects. However, poured concrete walls may have lower overall costs in terms of the total project due to factors such as excavation and finishing.
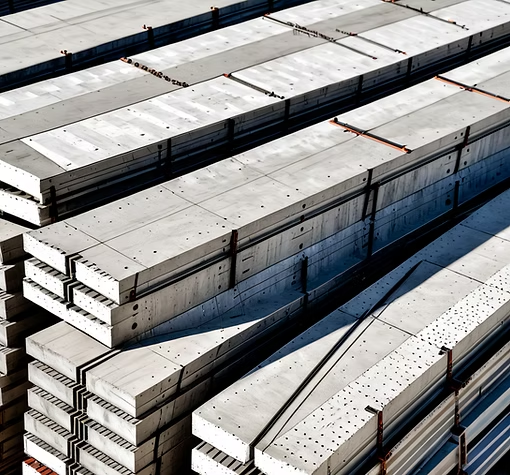
Cost per Square Foot
Understanding the cost per square foot for precast concrete is important for budgeting any construction project. This cost can vary depending on a myriad of factors including the complexity of the design, the size of the panels, and the location of the project.
Here’s how these costs break down in a more detailed format:
Type of Precast Concrete | Cost per Square Foot |
---|---|
Standard Precast Concrete Walls | $25 – $40 |
Average Precast Concrete | $150 – $320 |
Erection of Precast Panels (100 sq. ft.) | Approx. $30 |
Erection of Precast Panels (200 sq. ft.) | Approx. $20 |
General Precast Concrete | $6 – $15 |
Remember, these prices are averages and should serve as a general guideline. The final cost can be influenced by local market conditions and the specific details of a project. Always consult with a professional for an accurate quote.
Cost per Linear Foot
The cost per linear foot for structural precast concrete can vary, ranging from $43 for a 15-foot span to higher costs for longer spans. Factors influencing the cost include project location and design complexity. Additionally, the market value of the global precast concrete industry was estimated at USD 92.14 billion in 2020.
Understanding these influential factors is crucial when estimating the overall expenses for precast concrete construction. Proper planning and design can significantly impact cost efficiency, making it essential to consider all contributing elements to determine an accurate budget.
Average Total Cost
The average total cost of precast concrete varies widely due to factors such as dimensions, weight, delivery, excavation, engineering fees, installation, finishing, and design.
These costs can range from $25 to $40 per square foot for precast concrete walls and an estimated budget of $150 to $320 per square foot.
For precast panels or slabs alone, the cost ranges from $450 to $750 per cubic yard. Erection of precast panels could cost around $30 per square foot for a 100-square-foot panel and around $20 per square foot for a 200-square-foot panel.
The market value of the global precast concrete industry was recorded at USD 92.14 billion in 2020.
The wide range of costs highlights the importance of considering specific project needs when estimating the total expenses associated with using precast concrete products and structures. It’s crucial to carefully factor in all possible elements that contribute to overall costs so that accurate budgets can be determined before beginning any construction project involving such materials.
Ways to Lower the Cost of Precast Concrete
Consider getting multiple quotes from different suppliers to find the best price. Another way to lower cost is by choosing less expensive materials for your precast concrete project.
Getting Multiple Quotes
When looking to lower the cost of precast concrete, getting multiple quotes is crucial. By obtaining quotes from different suppliers and contractors, you can compare prices and negotiate for a better deal.
This allows you to ensure that you are receiving the best value for your investment. Additionally, comparing quotes can help you understand the average market price and identify any outliers in pricing, enabling you to make an informed decision.
Moreover, getting multiple quotes provides insight into the range of services offered by various providers and allows for a more comprehensive evaluation of factors such as delivery costs, material quality, and project timelines.
Choosing Less Expensive Materials
When choosing less expensive materials for precast concrete, consider options such as using aggregates that are locally available, which can help reduce transportation costs.
Additionally, optimizing the design to require fewer materials can lead to cost savings.
Using standard molds and reducing complexity in finishes can also contribute to lowering material expenses.
Selecting less expensive materials is crucial for cost-effective precast concrete construction. This can be achieved by sourcing materials from reputable suppliers and exploring alternative material options without compromising on quality or structural integrity.
Proper Planning and Design
To lower the cost of precast concrete, proper planning and design are essential. By carefully considering the shape, dimensions, weight, delivery, excavation, engineering fees, installation, finishing, and design aspects of the project upfront, significant cost savings can be achieved.
Additionally , choosing materials strategically and hiring experienced contractors also play a crucial role in reducing expenses. Proper planning ensures that potential issues are identified early on and addressed effectively to avoid costly rework while ensuring that designs are efficient in terms of material usage.
Considering all factors before the project begins has a direct impact on costs associated with precast concrete construction. Hiring professionals who understand how to properly plan and design a project will ensure long-term savings through optimal use of resources.
Hiring Experienced Contractors
When hiring experienced contractors for precast concrete projects, consider their expertise in handling the specific type of precast products required. Look for contractors with a proven track record in installing and erecting precast panels, beams, walls, and other elements.
Experienced professionals can ensure efficient construction practices and minimize costly errors, ultimately contributing to significant cost savings over the project’s duration.
Experienced contractors possess valuable insights into optimizing installation processes for precast components, leading to faster project completion and reduced labor costs. Their familiarity with local building codes and regulations can streamline approvals while mitigating potential delays or fines.
Additionally, seasoned contractors are adept at identifying cost-effective solutions without compromising quality standards or structural integrity.
Considering Long-Term Savings
Hiring experienced contractors is crucial for a successful precast concrete project. Aside from upfront costs, it’s important to consider long-term savings that can be achieved through the durability and low maintenance of precast concrete.
With its resistance to wear and tear, precast concrete requires minimal upkeep over its lifespan, reducing the need for frequent repairs and replacements. This can result in substantial cost savings over time, making it a wise investment for both residential and commercial construction projects.
Moreover, the energy efficiency of precast concrete contributes to long-term savings by providing better insulation properties compared to traditional building materials. This translates into reduced heating and cooling expenses, offering significant financial benefits over the years.
Conclusion
In conclusion, the cost of precast concrete planks can fluctuate based on various factors such as shape, dimensions, and delivery. Careful planning and design considerations can help in reducing expenses.
Ultimately, obtaining multiple quotes and hiring experienced contractors may lead to cost savings for precast concrete projects. Long-term savings should also be evaluated when considering the overall expense of utilizing precast concrete planks.
FAQs
1. What is the price of precast concrete planks per square foot?
Precast concrete plank prices typically range based on size and type but expect to see costs calculated per square foot.
2. Can I find a cost estimator for precast concrete planks?
Yes, use a precast concrete plank cost estimator or calculator online to get closer estimates for your specific project needs.
3. Are hollow core precast concrete planks more expensive?
Hollow core precast concrete planks may differ in price due to their design but can offer savings in construction expenses overall.
4. Does the cost of precast concrete vary by component, like beams or walls?
Indeed, each precast component, be it beams, walls, stairs, or panels has its own pricing structure based on material and labor costs.
5. Where can I find the closest pricing information for my area’s precast concrete plank cost?
For the most accurate local pricing details on the cost near you look up local vendors or request quotes from nearby suppliers specialized in providing these materials.
Recent Posts
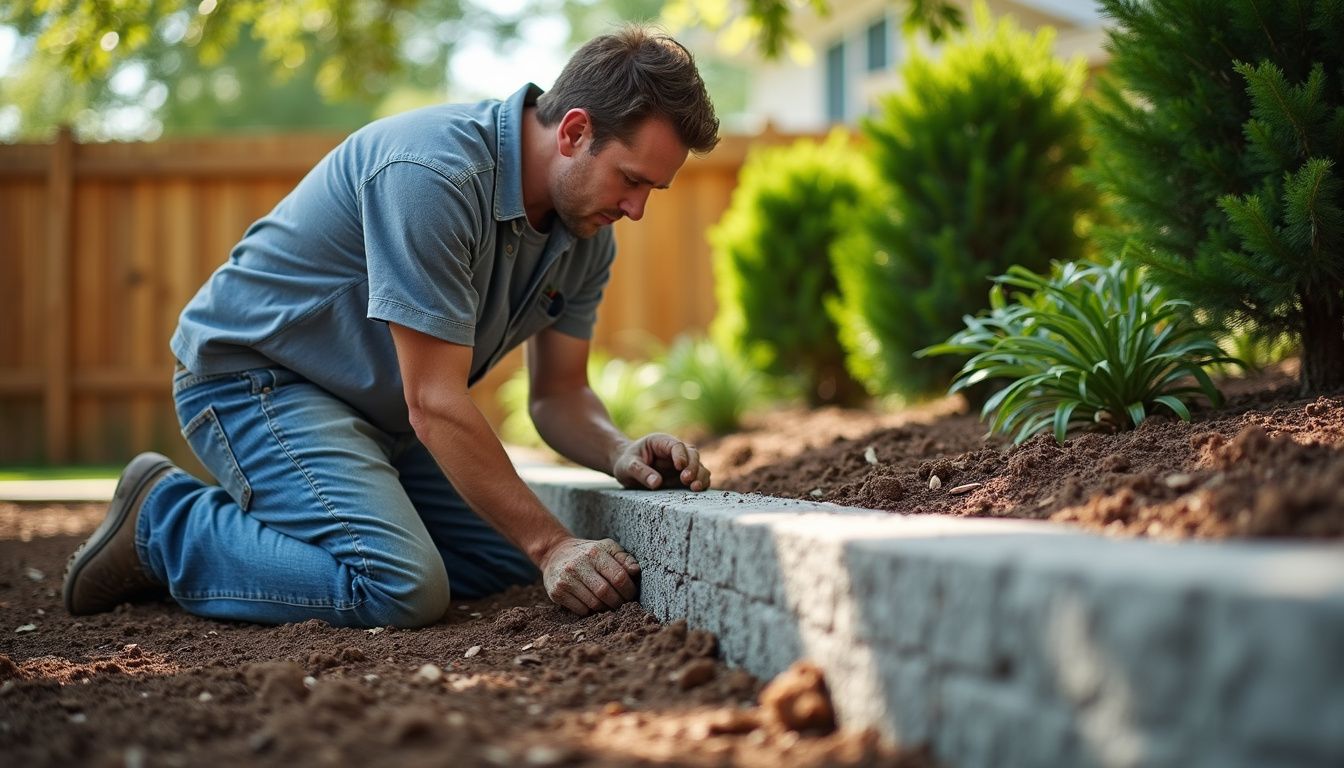
Why Landscaping Pros Prefer Precast Concrete Over Poured-in-Place
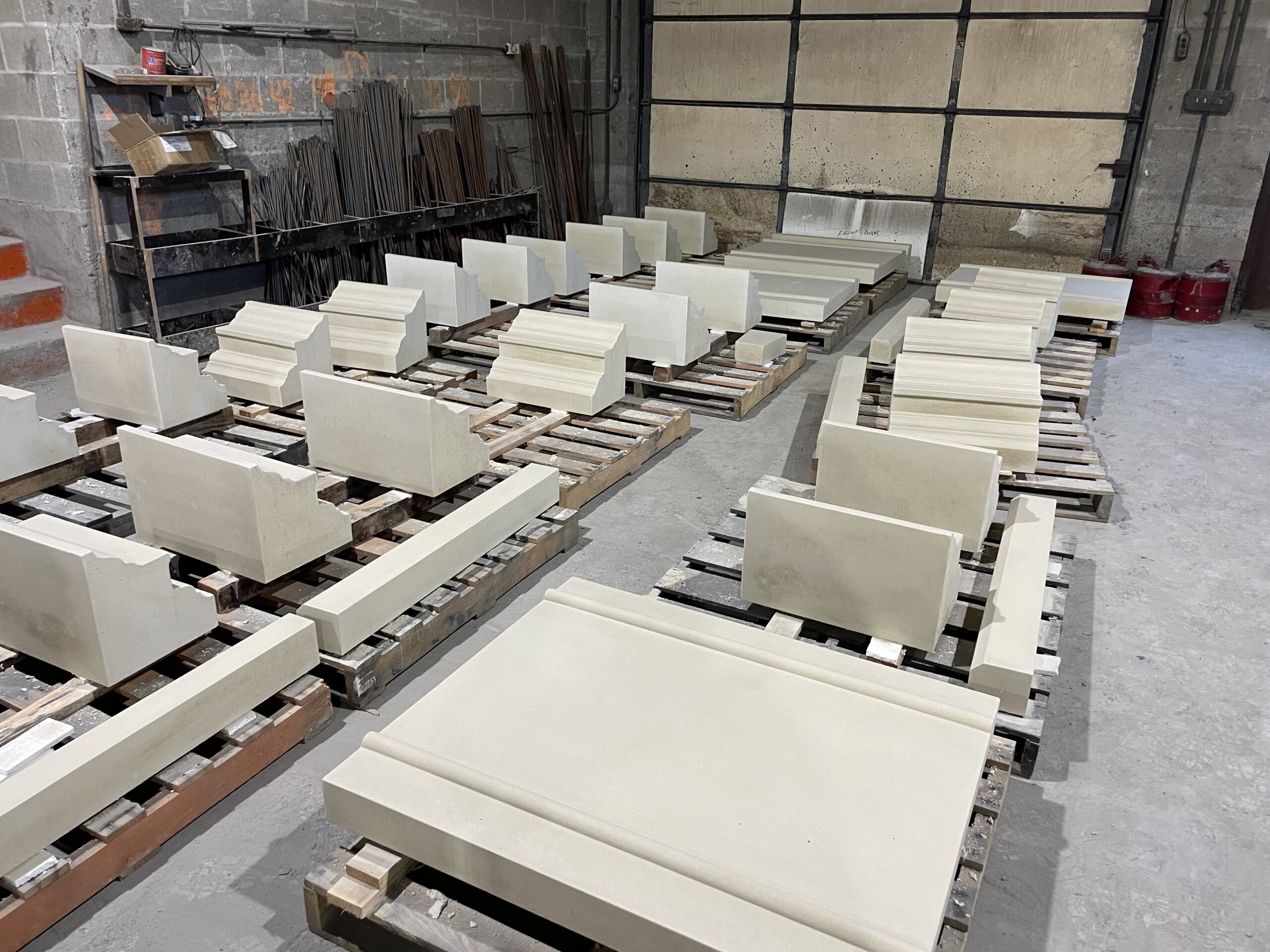
Why & How is Precast Concrete Prestressed?
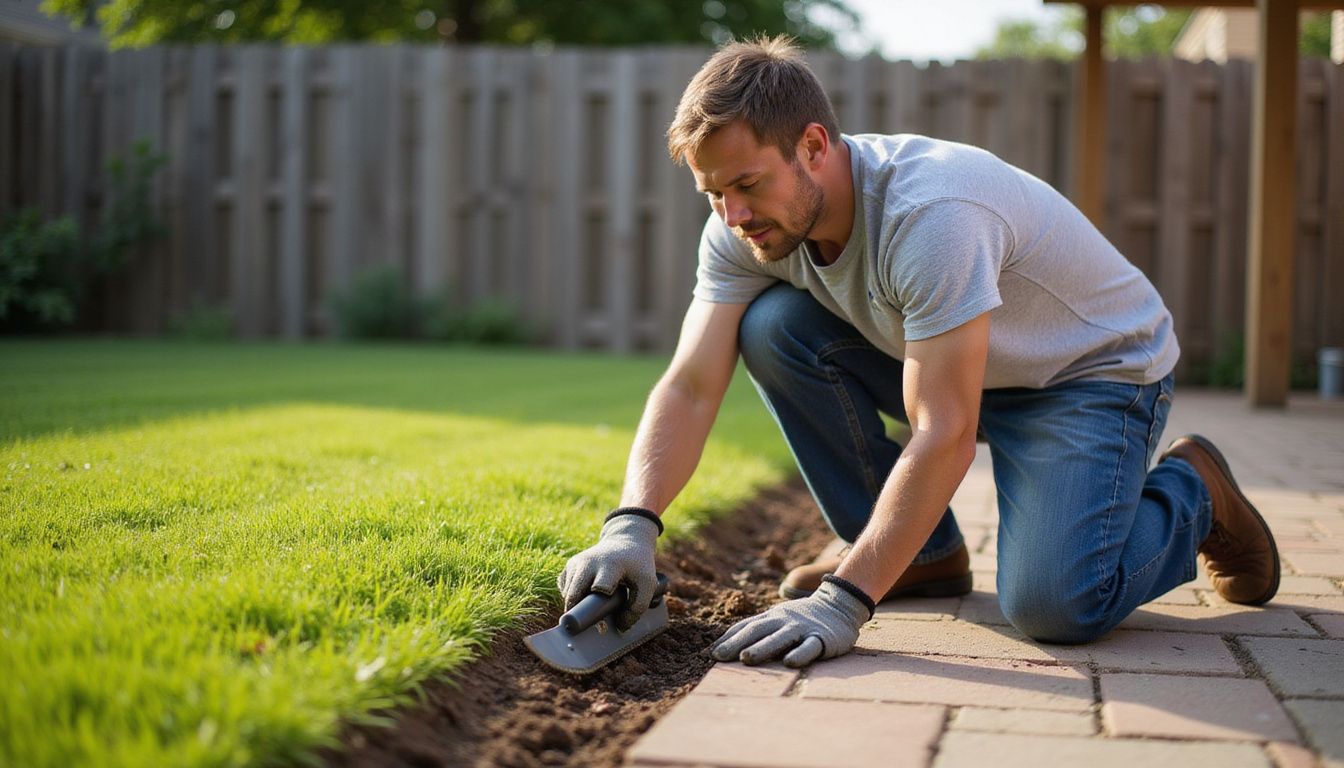